Your parking lot called — it wants its lines back! ☀️ Free Estimate — Call or Text 703-930-2200
Understanding Warehouse Striping for Efficiency
Warehouse striping improves organization and safety by marking loading zones, walkways, and storage areas—boosting workflow and efficiency in logistics facilities.
2023 BLOG
4/30/20255 min read
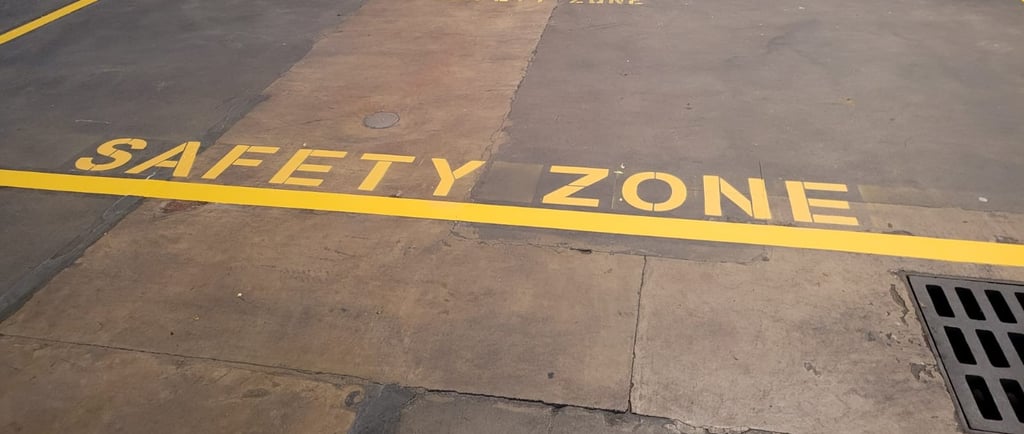
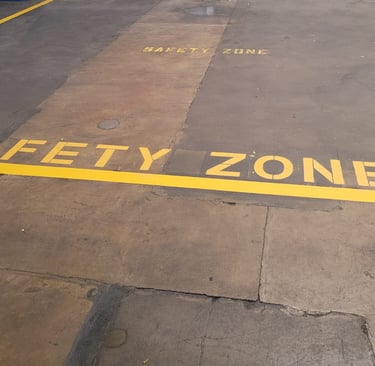
Understanding Warehouse Striping
Warehouse striping refers to the application of painted lines or markings on the floors of a warehouse or logistic facility. This practice is fundamental to the organization and management of warehouse space, as it not only designates specific areas for various functions but also enhances the safety and efficiency of operations within these environments. Clearly marked areas facilitate the movement of personnel and equipment, thus optimizing workflow and minimizing disruptions.
One of the primary functions of warehouse striping is the delineation of loading zones, which are crucial for the efficient handling of goods. These zones are designated areas where trucks and forklifts can safely load and unload inventory. The marked space ensures vehicles are parked in a way that does not obstruct traffic flow, reducing the likelihood of accidents. Moreover, having a clear visual indication of these zones helps warehouse employees quickly identify where to perform loading and unloading tasks, ultimately enhancing productivity.
Safety zones are another essential aspect of warehouse striping. These zones are engineered to keep pedestrians separate from moving equipment, particularly forklifts, which are a common sight in warehouses. By utilizing brightly colored lines and clear symbols, workers are reminded to remain within safe areas, thereby minimizing the risk of accidents and injuries. The implementation of safety zones serves not only to protect employees but also to instill a culture of safety within the workplace. Additionally, well-defined striping aids in compliance with industry regulations regarding safety protocols.
In conclusion, warehouse striping plays a pivotal role in logistics and warehouse management. By ensuring clear markings for loading zones and safety zones, organizations can significantly bolster operational efficiency and employee safety. The thoughtful application of these markings makes daily operations smoother and creates a secure working environment.
Techniques for Effective Marking
Effective warehouse striping is crucial for ensuring safety and efficiency within a storage facility. Various techniques can be employed to achieve optimal floor markings, with line chalking and adhesive striping tape being among the most commonly used methods. Each technique offers distinct advantages and disadvantages that can impact the overall effectiveness of the striping.
Line chalking is a method that involves using chalk-based substances to create temporary lines on the warehouse floor. This technique is advantageous due to its ease of application and removal, making it suitable for facilities that may require frequent reconfiguration of storage layouts. However, the durability of chalk lines can be an issue, particularly in high-traffic areas where wear and tear can quickly diminish visibility.
In contrast, adhesive striping tape offers a more permanent solution for floor marking. This method involves applying colored tape that adheres directly to the floor surface. The primary advantage of using tape is its durability; high-quality adhesive striping tape can withstand heavy foot and vehicle traffic, maintaining its visibility over time. However, one must be cautious when selecting tape, as not all options are created equal. Poor-quality tapes may peel or fade, necessitating premature replacement.
Additionally, the choice of paint can significantly affect the striping outcome. Acetone-based paints are popular due to their strong adhesion and vibrant colors. They provide a long-lasting solution, but their application requires proper ventilation and safety precautions due to the chemicals involved. Alternatives like water-based paints are more user-friendly and environmentally safe, but they may not offer the same level of durability as their acetone counterparts.
To achieve clean, straight lines regardless of the method chosen, using masking tape as a guide during the application process is advisable. Taking the time to measure and plan the layout beforehand can also enhance the overall effectiveness of the floor striping, ensuring that safety protocols are visual and easily distinguishable.
Removing Old Striping and Preparing for Reapplication
To ensure optimal safety and efficiency in a warehouse, effective removal of old adhesive striping tape is crucial before reapplication. The first step involves gathering the necessary tools and materials: a heat gun, scraping tools, acetone or adhesive remover, and protective gear. Begin by utilizing a heat gun to gently warm the old striping tape. This heat will soften the adhesive, making it easier to peel away. Once the tape has been heated adequately, use a scraping tool to lift the edges, gradually pulling the tape away from the floor.
If any adhesive residue remains after removing the striping, it can be challenging to achieve a clean surface for new markings. This step is where acetone-based products come into play. Dampen a cloth with acetone and apply it to the residual adhesive, allowing it to penetrate for a few minutes. After this time, use a scraping tool again to remove the softened residue, ensuring a clean and smooth surface. It's important to ventilate the area when using acetone to avoid inhalation of fumes, and to wear gloves to protect your skin.
Once the old striping and adhesives are removed, the preparation of the warehouse floor for new markings can commence. A thorough cleaning is essential to eliminate dust, dirt, and any remaining chemicals from the surface. Utilize a floor scrubber or a mop with a suitable cleaning solution for this endeavor. After the floor has dried completely, inspect it for any imperfections, such as cracks or holes, that may need repair before new striping applications. Proper surface preparation not only ensures the longevity of new markings but also contributes significantly to the overall safety standards within the warehouse environment. By meticulously following these steps, facilities can achieve a smooth and effective transition from old to new striping, reinforcing safety and operational efficiency.
Maintaining Warehouse Markings for Long-Term Safety
Maintaining warehouse striping is vital for ensuring long-term safety and operational efficiency within a facility. Over time, the wear and tear on floor markings can diminish their visibility, leading to confusion and potential accidents. Therefore, regularly assessing the condition of existing markings is essential. Observing the state of the striping should be integrated into routine safety checks, which can help identify whether the markings have faded or become obscured due to dust, spills, or heavy usage.
Understanding when to refresh or redo warehouse striping is crucial. A general recommendation is to evaluate the striping every three to six months, paying close attention to high-traffic areas. Factors such as the type of flooring, traffic volume, and exposure to harsh chemicals can influence how often the markings need maintenance. If the colors are dull or if the paint is chipping away, a refresh is necessary to uphold visual clarity and safety standards. Additionally, implementing a proactive refresh timetable aligns with safety regulations and best practices within the industry.
Establishing a regular maintenance routine is instrumental for ongoing safety compliance. This could involve assigning specific staff members the responsibility of inspecting the markings and taking corrective action as needed. Utilizing clear checklists can facilitate systematic evaluations, making it easier for employees to report issues. Furthermore, incorporating these measures into training programs fosters a culture of safety among workers, emphasizing the collective responsibility toward maintaining a safe warehouse environment.
In conclusion, prioritizing the maintenance of warehouse striping not only enhances safety but also promotes operational efficiency. A well-maintained warehouse environment creates clarity, reduces accidents, and ensures compliance with safety regulations, ultimately contributing to a more productive workplace.
We are happy to answer any of your striping questions. As a leading painting contractor serving DC, Maryland, and Northern Virginia, we are dedicated to delivering high-quality results. Contact us today for a free estimate and see how we can enhance your parking areas.
Contact Us
Phone
703-930-2200
info@potomacstriping.com
Address
Reston, Virginia 20191
Serving: District of Columbia, Montgomery County, Prince George's County, Arlington County, Fairfax County, Loudoun County, Prince William County, the City of Alexandria, the City of Fairfax, the City of Falls Church, the City of Manassas, City of Manassas Park, Richmond and Charlottesville.
Potomac Falls Striping Services Copr. 2025